Home
ReducedEffort® Changeover: The Lean Way to Quickly Reduce Changeover Downtime, Second Edition
Loading Inventory...
Barnes and Noble
ReducedEffort® Changeover: The Lean Way to Quickly Reduce Changeover Downtime, Second Edition
Current price: $39.99
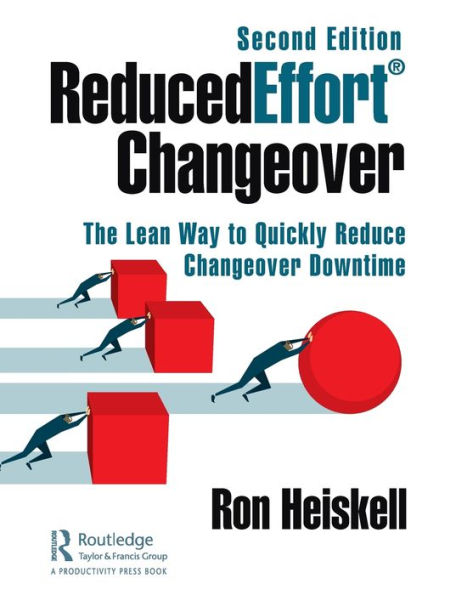
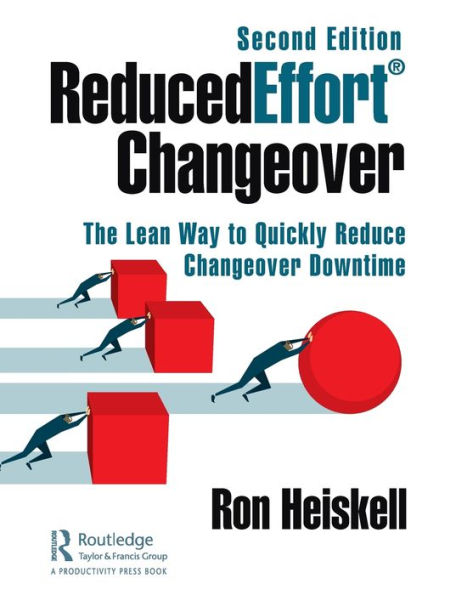
Barnes and Noble
ReducedEffort® Changeover: The Lean Way to Quickly Reduce Changeover Downtime, Second Edition
Current price: $39.99
Loading Inventory...
Size: OS
*Product Information may vary - to confirm product availability, pricing, and additional information please contact Barnes and Noble
ReducedEffort® Changeover: The Lean Way to Quickly Reduce Changeover Downtime
provides a step-by-step guide for conducting a Kaizen event that empowers the people who do the work to improve how that work is done. Packed with tips, tools, and examples, this practical guide begins with a clear description of the Lean principles underlying the ReducedEffort Changeover system. In addition, it explains how and why reducing the effort always reduces the time of converting a machine, line, or process from one product to another. In this book, you’ll find everything you need to quickly and dramatically reduce the effort and time of any process using the ReducedEffort method.
This is not another book about how to do SMED. Like SMED, ReducedEffort Changeover (REC) does reduce changeover time, but REC is not SMED.
SMED, Single Minute (or digit) Exchange of Dies, developed by Dr. Shigeo Shingo, has been the process used for many years by countless manufacturing plants to reduce changeover time. The SMED process was used in Toyota to reduce the changeover of a 1,000-ton stamping press from four hours to three minutes.
As a Lean-based process, the REC system focuses on reducing the labor, not the time, involved in changing over a machine to work on a different product. With REC, there are no Standard Operation Combination Sheets to fill out and no Problem Identification Sheets to complete, and it does not require the arduous chore of timing every task, as SMED does.
Very little capital investment is required with REC. Unlike SMED, it does not require management-approved funding to achieve substantial results. Because REC is not capital-driven, management does not need to drive the process. The operators will drive the process because it reduces their labor. One of the biggest advantages of REC over SMED is that operators will readily accept the process, and more important, they will want to sustain it. The reason for this is quite simple and will become evident when the REC process is defined. REC takes SMED to a new level that is easier and faster both to implement and to deliver sustainable results.
provides a step-by-step guide for conducting a Kaizen event that empowers the people who do the work to improve how that work is done. Packed with tips, tools, and examples, this practical guide begins with a clear description of the Lean principles underlying the ReducedEffort Changeover system. In addition, it explains how and why reducing the effort always reduces the time of converting a machine, line, or process from one product to another. In this book, you’ll find everything you need to quickly and dramatically reduce the effort and time of any process using the ReducedEffort method.
This is not another book about how to do SMED. Like SMED, ReducedEffort Changeover (REC) does reduce changeover time, but REC is not SMED.
SMED, Single Minute (or digit) Exchange of Dies, developed by Dr. Shigeo Shingo, has been the process used for many years by countless manufacturing plants to reduce changeover time. The SMED process was used in Toyota to reduce the changeover of a 1,000-ton stamping press from four hours to three minutes.
As a Lean-based process, the REC system focuses on reducing the labor, not the time, involved in changing over a machine to work on a different product. With REC, there are no Standard Operation Combination Sheets to fill out and no Problem Identification Sheets to complete, and it does not require the arduous chore of timing every task, as SMED does.
Very little capital investment is required with REC. Unlike SMED, it does not require management-approved funding to achieve substantial results. Because REC is not capital-driven, management does not need to drive the process. The operators will drive the process because it reduces their labor. One of the biggest advantages of REC over SMED is that operators will readily accept the process, and more important, they will want to sustain it. The reason for this is quite simple and will become evident when the REC process is defined. REC takes SMED to a new level that is easier and faster both to implement and to deliver sustainable results.